Solving phosphorus removal challenges with magnetite ballasted technology at Billerica Wastewater Treatment Facility, MA, USA
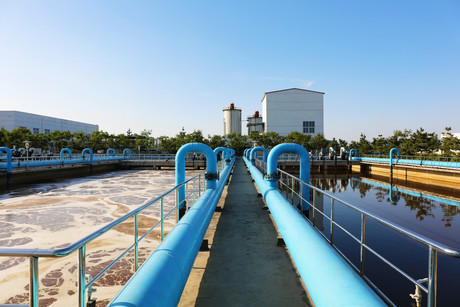
By Michael Casey Whittier1, Jeffery Kalmes2, Raymond Pepin1, Sam Towndrow3
1. Evoqua Water Technologies, Tewksbury, MA, United States
2. Plant Superintendent, Town of Billerica, MA, United States
3. Evoqua Water Technologies Pty Ltd., Sydney, Australia
Abstract
The Town of Billerica is located in Middlesex County, Massachusetts, and owns and operates the town’s wastewater treatment facility (WWTF). In 2005 a revision of the plant environmental discharge licence required the plant meet a more stringent monthly average limit of 0.2 mg/L total phosphorus (TP) and mandated that the plant undertake the required upgrades to achieve this within a four-year time frame. A number of options were evaluated but following successful pilot trials, CoMag® ballasted coagulation was selected as the preferred solution due to its ability to meet even more stringent future effluent targets down to 0.05 mg/L total phosphorus, deal with wide fluctuations in flow, influent phosphorus and total suspended solids all within a compact footprint. This paper explains how magnetite ballasted technology came to be selected and presents almost eight years of operational experience and performance data.
Introduction
The Town of Billerica is located in Middlesex County, in the north-eastern corner of Massachusetts, USA. The town owns and operates the wastewater treatment facility (WWTF), along with all pump stations and collection lines. The original facility was constructed in 1966 with upgrades in 1975, 1982, 1984, 1988 and the CoMag ballasted coagulation tertiary treatment system in 2010. The Billerica influent stream is primarily residential with no significant industrial or commercial contribution and treated effluent is discharged into the Concord River.
Following revision of the facility’s effluent discharge licence, Billerica was required to improve the treatment plant’s total phosphorus removal capacity to meet a new discharge limit of 0.2 mg/L with the possibility of even lower TP limits in the future.
A range of process options were assessed, including converting the plant to an Enhanced Biological Phosphorus Removal (EBPR) process; however, this would still not be certain to achieve a future limit of 0.1 mg/L Total Phosphorus. For this reason the town decided a tertiary treatment solution was the best approach.
The CoMag system was piloted on-site in the summer of 2007, and successfully demonstrated the capability to comfortably meet the 0.20 mg/L permit limit with alum, polyaluminium chloride (PACl), ferric chloride or sodium aluminate coagulants. Additionally, the pilot demonstrated that future permit limits as low as 0.05 mg/L could also be met without the need for a polishing filter by simply increasing the coagulant dose.
As evidenced by Figures 1 and 2, the effluent TP limit of 0.2 mg/L was met throughout the pilot testing period, for both ferric chloride and alum. The pilot also demonstrated that if effluent TP limits were to be eventually reduced to as low as 0.05 mg/L, the CoMag system was capable of operating below this point without the need for post filtration.
Another factor for consideration was the limited available space on-site, meaning a compact solution was preferable. Additionally, there were two existing unused concrete tanks that either needed to be demolished or repurposed and ultimately, it was the ability to repurpose these tanks, saving demolition and construction costs, coupled with the successful pilot trials, that led to selection of the magnetite ballasted CoMag system solution.
The magnetite ballasted system
CoMag system is a high rate ballasted clarification process utilising chemical coagulation along with magnetite, a ballasting agent which becomes embedded within the chemical floc and provides rapid settling to enhance TP and TSS removal. The system process flow diagram is shown in Figure 3.
Influent flow is measured to pace coagulant and polymer, along with the recycle and waste rates. Coagulant and caustic for pH control is injected inline prior to the coagulation tank where conventional chemical coagulation/floc formation occurs. The resultant pH is measured at the inlet of the coagulation tank. Gentle mixing and a design HRT of 6 minutes at average daily flow allows for a stable chemical floc to be formed. The wastewater and flocs pass over a baffle into the ballast mix tank, where internally recycled sludge (which contains residual coagulant and polymer) and magnetite from the clarifier is re-used and recovered magnetite from the magnetic recovery drum is returned. The ballast tank has an HRT of 3 minutes at average daily flow. A VFD controlled mixer allows for the proper mixing energy to ensure magnetite embedment into the chemical floc without applying too much mixing energy and breaking up the floc.
An underflow baffle separates the ballast and polymer tanks. Polymer is added in the polymer tank to enhance floc formation and to allow for rapid settling in the clarifier. The polymer tank also has an HRT of 3 minutes at average daily flow. A VFD controlled mixer provides proper mixing energy for optimum flocculation and prevention of floc settling prior to the clarifier without applying too much mixing energy and breaking up the floc.
Two, seven-metre diameter, four-metre side wall depth clarifiers provide adequate surface area for sedimentation to occur. An inline CoMag system effluent turbidity meter provides real-time effluent turbidity monitoring and is used for process monitoring and adjustment because turbidity has been found to be a good surrogate indicator of effluent TP and other contaminants. The effluent overflows to the chlorine contact chamber (CCC).
Settled sludge is both wasted and recycled internally using a single centrifugal pump. Flow control valves, coupled with recycle and waste sludge flow meters, allow for recycle and waste flows to be flow paced or set manually. Waste flow is sent through an inline shear mixer prior to the magnetic recovery drum where the ballast is separated from the floc. The recovered magnetite from the magnetic recovery drum drops into a slurry tank and is pumped back to the ballast tank. Unballasted waste sludge from the drum flows by gravity to a gravity sludge thickener where it is blended with the facility’s other primary/biological/chemical sludge. The combined sludge is then dewatered using a rotary sludge press.
Magnetite is hydrophobic and has a specific gravity of 5.2, which substantially increases the settling rate of the chemical floc. By increasing the settling rate, the magnetite ballasted process requires a smaller footprint to treat equivalent flow rates when compared to conventional systems.
An integral part of the process that enables it to high quality effluent with a lower coagulant and polymer dose than alternate processes is the ability to internally recycle the ballasted sludge without breaking up the floc. This enables the system to:
- Maintain a thick and effective magnetite and solids concentration.
- Utilise the residual coagulant and polymer in the recycled sludge to enhance the co-precipitation effect of the metal hydroxide and phosphate floc, thus reducing coagulant and polymer dose requirements.
- Increase the density of the floc particles in the reaction tanks by recirculating them to further increase the density of the flocs (sludge densification) and to allow for increased absorption/adsorption of soluble contaminants into the flocs.
Full-scale system operation 2010 to 2018
Billerica WWTF
The Billerica WWTF is a conventional activated sludge plant consisting of the following process units: screening, grit removal, primary clarification, activated sludge with diffused aeration, secondary clarification, magnetite ballasted tertiary precipitation, disinfection and post aeration. Plant size is summarised in Table 1.
Item | Value |
Design capacity | ADF = 20.4 ML/d MDF = 54.1 ML/d PHF = 62.5 ML/d |
Primary clarifiers | 3 x 18.3 m diameter |
Aeration basins | 2 x 3333 m |
3 Secondary clarifiers | 4 x 18.3 m diameter |
CoMag reaction tanks | 4 x 40 m3 (in series) |
CoMag clarifiers | 2 x 7 m diameter |
The design basis for the full-scale magnetite ballasted tertiary system is presented in Table 2.
Start-up, optimisation and performance test
Based on the pilot plant results, the Billerica WWTF decided to use alum as their coagulant. The average CoMag system alum dose during this period was 3.0 mg/L as Al. The full-scale Billerica system was “charged” with magnetite and started up for the first time on 7 September 2010. The system had a successful start-up and began meeting the effluent TP limit within minutes after initial coagulant and magnetite addition. The system was then allowed to come into equilibrium overnight; equipment check outs, process optimisation and effluent testing began the next day.
The test results from the first 33 effluent TP tests conducted during the 2-week optimisation and adjustment period are illustrated in Figure 4. The system responded exactly as designed and generated results were well below the effluent total phosphorus monthly average limit of 0.20 mg/L. Effluent TPs were stable and ranged from 0.036 to 0.12 mg/L (0.055 mg/L average).
Immediately after the process optimisation and adjustment phase described above, the CoMag system was deemed ready for the formal performance acceptance test phase. However, the effluent TPs generated during the initial start-up phase were significantly lower than those required for the performance tests and the process settings were ‘detuned’ to produce higher effluent TPs, but still remain comfortably below the permit limit of 0.20 mg/L. Formal performance and acceptance tests were conducted over 15 days. The objective of these tests was not to generate the lowest possible effluent TPs but to demonstrate a reliable level of performance consistency with effluent TPs below the permit limit and achieve an average effluent TP target of <0.10 mg/L.
The results of this test phase are displayed in Figure 5. Effluent TPs ranged from 0.043 to 0.135 mg/L (0.085 mg/L average). The average alum and polymer dose during this test period was 3.5 mg/L as Al and 0.90 mg/L, respectively.
On many days during these tests, the CoMag system was subjected to several influent flow surges when the feed flow increased by a factor of three during the course of less than 1 minute without serious impacts on the CoMag system effluent quality. These surges were caused by instrumentation control issues in the WWTF main pump station that feeds the CoMag system.
It was not part of the test plan; however, after the CoMag system began running 24/7, Billerica operations staff noted that the effluent ammonia nitrogen test results began to run at half of what was their previous experience. Ammonia nitrogen had previously been between 5 to 6 mg/L and they were now measuring 2 to 3 mg/L of ammonia nitrogen while the CoMag system was operating.
Full-scale operating results
The facility has seasonal effluent TP limits that dictate the mode in which the CoMag system is operated throughout the year. The winter and summer TP limits are 1.0 and 0.2 mg/L, respectfully. During the summer the CoMag system is operated in the same fashion as it was during process start-up and performance testing, ie, all flow is passed through the CoMag system to ensure that the desired level of TP reduction is met.
During the winter TP season, Billerica splits the flow from the secondary clarifier utilising the splitter box. A constant flow rate of approximately 5.9 MLD is drawn from the splitter box and is pumped to the CoMag system 24/7. All excess wastewater flows by gravity and bypasses the CoMag system to disinfection. The flow which passes through the CoMag system averages approximately 35% of the total flow. The CoMag system effluent then blends with the bypassed wastewater before disinfection.
Figure 6 displays monthly average effluent TPs for 2014 through 2018 and illustrates the wide range of capability generated by blending flows during the winter. The tertiary CoMag system also produced significant further reductions in secondary effluent BOD and TSS. The average additional BOD and TSS reductions during this period were 59% and 38%, respectively. The average daily flow during this same period was 14.3 MLD.
Manpower requirements are minimal and less than 30 minutes per day. Prior to the installation of the CoMag system, the WWTF was staffed 24/7 with three shifts. After the CoMag system came online and demonstrated its reliability, the WWTF began operating only with a day shift.
The average Billerica CoMag magnetite consumption rate has been 25 pounds per day. Based on an average daily flow of 14.3 MLD, this is equivalent to 7 pounds of magnetite, ie, less than a shovel a day, consumed per million gallons treated. Plant staff monitor the CoMag sludge recycle pumps for any signs of seal or impeller wear. The process has been running continuously since September of 2010 and as of January 2018, these pumps have been performing dependably with no signs of wear or abrasion.
Conclusion
The Billerica, Massachusetts WWTF magnetite ballasted CoMag system has proven to be a reliable and versatile tertiary treatment option that has the capability to be dialled in to achieve any effluent TP target down to <0.050 mg/L, while also achieving significant reductions in TSS, BOD and other contaminants. The system has provided Billerica the flexibility to meet and exceed both current and any future total phosphorus permit discharge limits.
Acknowledgements
Jeffrey Kalmes, Superintendent, Town of Billerica Wastewater Treatment Facility
For further information, please contact: 1300-661 809 or info.au@evoqua.com.
From Crisis to Control: AI Offers New Hope for Water Management
Oldcastle Infrastructure has developed CivilSense, a cutting-edge water infrastructure asset...
Wannon Water Solves Pump Blockage Issue
Wannon Water replaced some old digester pumps at its Hamilton wastewater treatment plant with new...
Gippsland Water eliminates pump blockages at Morwell WWTP
At the Gippsland Water Morwell Waste Water Treatment Plant, the company have utilised two Gorman...