Minimising water treatment plant degradation and chemical spills
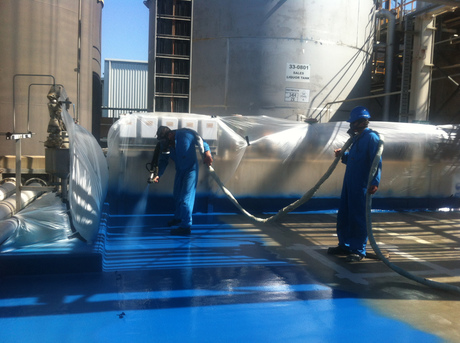
For more than half a century, companies have invested billions of dollars into equipment and infrastructure to process wastewater and sewage. Corrosion of this infrastructure — and, in some cases, the subsequent leakage — costs industry over $1 billion each year.
The main assets that are impacted by corrosion in wastewater treatment plants are the pipelines, storage tanks, clarifier ponds and sewage channels. One method of refurbishing these assets is to carry out surface repairs and then apply protective coatings. These coatings must be strong, flexible and resistant to chemical attack.
Special consideration is required when coating structures in sewage treatment plants, according to Rhino Linings Australasia (RLA) Special Projects Engineer Dennis Baker. Baker explained that one of the more corrosive by-products of sewage is hydrogen sulfide gas, stating, “Hydrogen sulfide reacts with moisture on surfaces in a wastewater plant and bubbles up to form sulfuric acid, which really loves concrete.”
Hydrogen sulfide attacks the cement, copper, iron and silver, which gradually degrades the structure. In the case of a pipeline, this may ultimately result in the collapse of the pipe wall. In addition, the flammable, colourless gas also poses a health risk to workers.
One type of coating from RLA that is suitable for wastewater treatment is spray-applied polyurea and, more recently, pure polyurea. Pure polyureas are formed when a liquid isocyanate is mixed with an amine-based resin solution. Isocyanates are reactive because the double covalent bond attaching the carbon atom to nitrogen and oxygen atoms is easily broken to form single bonds in the more stable tetrahedral configuration around the carbon atom.
RLA pure polyurea comes as a two-part solution that is mixed under high temperature and pressure (3000 psi at 65°C) in a specially designed spray apparatus. When applied, the chemical crosslinking produces a dense but flexible surface. The high density makes the coating almost impervious to abrasion, water and chemicals.
Pure polyurea coatings ‘snap cure’ to form a solid surface in a few seconds and can be walked on without damage in less than a minute. According to Baker, “Unlike all other coatings, pure polyureas are not affected by ambient moisture or temperature. We can return a facility to service in four hours, with full cure in 24 hours.”
Whereas epoxies and paints form a solid rigid shell, the flexibility of polyurea coatings allows them to move with the expansion and contraction of the underlying structure as temperatures change. It can be sprayed at very high thickness (6000 µm and greater) on a sloping or vertical surface without sagging or running. The surface of an RLA coating is easy to maintain, clean and recoat if necessary.
The chemicals utilised in polyurea and pure polyurea coatings mean that most of the work carried out by RLA applicators, such as Queensland-based Satintouch, is defined as an environmentally relevant activity (ERA) under government legislation. The owner and managing director of Satintouch, Scott Blair, said RLA serves as “a great resource for us, especially for advice as to what can or should be done on a project”.
Satintouch’s teams usually consist of three technicians and a supervisor working on-site, along with an independent QA/QC inspector who oversees projects and ensures all procedures are followed and documentation prepared according to requirements and specifications. This includes the RLA procedures as well as the rules and guidelines of the ERA legislation.
For projects involving heavy traffic and wear, Blair said Satintouch will usually install an indicator layer which is bright red before the final top coat. Once the red layer starts to show through the main coating, it is clear that the structure or surface will need re-covering soon. Recording these wear rates enables better protection planning.
The durability of pure polyurea and polyurea as surface protection means that money can be saved because the structure has a longer repair/replace cycle. “Polyurea coatings are also easy to repair,” Baker said. “The area around a damaged surface can be reactivated using special primers and then covered with a new layer of polyurea.”
RLA’s formulations, combined with innovative substrate preparations, result in good adhesion and a seamless surface over virtually any shaped structure. “Applied correctly, our spray-applied polymer coatings have attachment loads of at least 6 to 10 mPA (750 to 1250 psi),” said Baker. “In most cases, the concrete substrate would give way before the coating peeled off.”
Spray-applied pure polyurea and polyurethane from RLA offer suitable solutions for liquid containment. All coatings developed by the company for the water industry are continually tested to ensure they comply with the latest standards and have been certified safe for applications such as lining potable water storage tanks, marine aquariums, food freezers and grain silos.
The coatings are covered by long guarantees, with water treatment facilities extending to 20 and 25 years’ warranty. Blair also has a personal routine for client follow-up where he contacts as many customers as practical every two years, “just to make sure everything that we installed and coated still meets their requirements and that there have been no failures”, he said.
Phone: 07 5585 7000
Rosemount 490A optical dissolved oxygen sensor
The sensor is a digital Modbus-enabled measurement device designed to improve operational...
Kaeser GBS series rotary screw blowers
This range of blowers offers high efficiency and low maintenance and is suitable for applications...
Odosense Odour Emissions Tracking System
Odosense is an active odour analysis and public complaint validation system, which is suitable...