From mixed plastic to fuel: improving the process
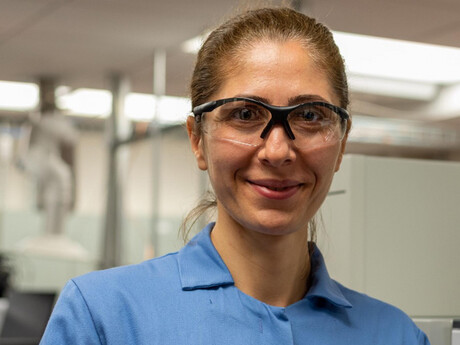
A strategy for addressing Earth’s growing plastic pollution problem is turning plastic waste into useful products. A study has found it may be possible to improve one method, called pyrolysis, to process hard-to-recycle mixed plastics — like multilayer food packaging — and generate fuel as a by-product.
Pyrolysis involves heating plastic in an oxygen-free environment so the materials break down and create new liquid or gas fuels. Current commercial applications of pyrolysis either only operate below the necessary scale or handle certain types of plastics.
“We have a very limited understanding of mixed-plastic pyrolysis,” said Hilal Ezgi Toraman, assistant professor of energy engineering and chemical engineering at Penn State (pictured). “Understanding the interaction effects between different polymers during advanced recycling is very important while we are trying to develop technologies that can recycle real waste plastics.”
The scientists conducted co-pyrolysis of two of the most common types of plastic, low-density polyethylene (LDPE) and polyethylene terephthalate (PET), along with different catalysts to study the interaction effects between the plastics. They found one catalyst may be a good candidate for converting mixed LDPE and PET waste into valuable liquid fuels. Catalysts are materials added to pyrolysis that can aid the process, like inducing the plastic to break down selectively and at lower temperatures.
“This type of work can allow us to provide guidelines or suggestions to industry,” Toraman said. “It’s important to discover what kind of synergies exist between these materials during advanced recycling and what types of applications they may be right for before scaling up.”
LDPE and PET are commonly found in food packaging, which often has various layers of different plastic material to keep products fresh. These are generally difficult to recycle with traditional processes because each layer has to be separated. According to Toraman, pyrolysis can handle the complexity of these materials.
The first step to developing new commercial pyrolysis processes is having a better mechanistic understanding of how plastic waste mixtures decompose and interact.
The scientists conducted pyrolysis on LDPE and PET separately and together, observing interaction effects between them during tests with each of the three catalysts they used.
“We saw products that can be very good candidates for gasoline application,” Toraman said.
The team developed a kinetic model that was able to showcase the interaction effects observed during the co-pyrolysis process. Kinetic models attempt to predict the behaviour of a system and are important for better understanding why reactions are occurring.
“Systematic and fundamental studies on understanding reaction pathways and developing kinetic models are the first steps toward process optimisation,” Toraman said. “If we don’t have our kinetic models right, our reaction mechanisms accurately, then if we scale up for pilot plants or large-scale operations, the results won’t be accurate.”
Toraman would like the research to lead to better environmental responsibility in the recovery, processing and utilisation of Earth’s resources.
REDWAVE TEX textile sorting solution
The REDWAVE TEX is a flexible sorting solution designed specifically for the textile industry.
PCO.Tech pco.pixelfly 1.3 SWIR camera
The pco.pixelfly 1.3 SWIR is a machine vision camera with an InGaAs image sensor that is...
Emi Controls V12so Odour Control Cannon
The V12so Odour Control Cannon combines four different functions in one machine — eliminate...