Evolution of SEW-EURODRIVE decentralised drive technology
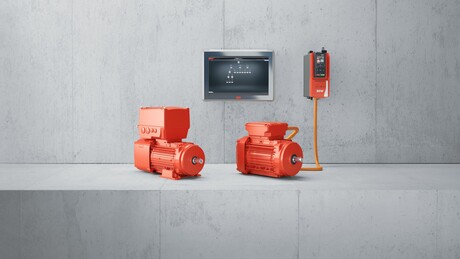
By integrating a new decentralised inverter with a tried and tested motor, SEW-EURODRIVE has taken the next step in the evolution of decentralised drive technology. In doing so, the global designer and developer of mechatronic transmission systems and motor control electronics has created an ‘all-rounder’ drive unit. Early adopters have already deployed the drives widely in Australia, and SEW-EURODRIVE is set to ramp up to full scale local assembly in 2024.
Known as MOVIMOT® advanced, the drive unit covers a power range from 0.37 to 7.5kW with the ability to achieve the highest efficiency standards. The integration of an IE3 asynchronous motor or an energy-efficient IE5 synchronous motor means that the decentralised drive unit achieves the maximum system efficiency IES2 – widely regarded as the gold standard for energy efficiency of drive systems.
Applications everywhere
According to Francois Sieberhagen, SEW-EURODRIVE National Product Engineer – Product Management, MOVIMOT® advanced displays all the characteristics of a true all-rounder. He says that with a high overload capability, and options such as brakes and encoders, the drive units have a multitude of uses. “Applications such as conveyors, simple lifts and positioning axes are all possible,” he says. “This means the drive units are suitable in a wide range of industries, from manufacturing and materials handling to waste management.”
As part of the MOVI-C® range, MOVIMOT advanced is compatible with SEW-EURODRIVE’s existing range of 7-series and 9-series gearmotors, which Sieberhagen says are widely used in industry and renowned for their quality, reliability and robustness. The mechanical interface to the customer’s machines therefore remains identical. This allows users to make use of existing machine designs and install the drive units at new plants or retrofit to existing equipment.
MOVI-C is the name given to SEW-EURODRIVE’s latest modular automation portfolio. It consists of inverter technology, drive technology, control technology and engineering software. “This provides complete automation from a single source and automation specialist,” says Sieberhagen.
Control cabinet or decentralised
The MOVI-C portfolio offers both control cabinet and decentralised technology. The new decentralised range consists of four product families: MOVIMOT® advanced, MOVIMOT® flexible, MOVIMOT® performance and MOVIGEAR® performance. All four use an identical decentralised inverter, regardless of whether it is installed close to the motor or integrated into an asynchronous or synchronous motor. Sieberhagen says this makes the user experience consistent throughout all product families.
When the decentralised version of MOVI-C is chosen, the control and inverter technology is no longer installed inside a control cabinet, but in the field, mounted onto or within close proximity to the motor. Sieberhagen says this reduces the need for costly control cabinets, cabinet cooling and long motor cabling. It improves electromagnetic compatibility (EMC), reduces the installation time and effort, and results in a more energy-efficient system due to less cable losses.
“So, whether their system is centralised, decentralised, or a combination of both, our customers can plan the design of their machines with the same communication topology,” he says. “They can integrate both centralised and decentralised within the same network or interchange from centralised to decentralised seamlessly.”
Once installed, the MOVIMOT advanced can be isolated for maintenance purposes, due to its optional integrated load disconnector. Sieberhagen says this maintenance switch can be used to disconnect the supply voltage from the decentralised inverter without the entire system being shut down. This allows users to conduct planned maintenance or replace the device while keeping their plant running as normal.
Secure data transfer
Modern safety requirements in production environments have led to changes in the approach to the safe operation of machinery. In the past, it was sufficient to hardwire safety equipment into machines. For example, an emergency stop button may have been the main feature. Nowadays, it is more common to take an integrated approach to safety. As a result, safety-related data needs to be transferred in a secure manner.
The entire MOVI-C decentralised family can optionally operate with a field bus system such as PROFINET, EtherNet/IPTM and Modbus TCP. However, the newer approach to safety demands safety-oriented field buses, often referred to as ‘black channels’. MOVI-C offers the safe protocols Profisafe, CIP Safety, and FSoE as options for the transfer of safety-related data across networks. This eliminates the need for additional hard wiring.
Simplified setup
MOVIMOT advanced is equipped with MOVILINK® DDI as standard. Sieberhagen says this digital motor interface with electronic nameplate contains all drive data. “There’s no need for manual motor start-up, and this saves valuable time,” he says.
The MOVI-C controller and inverter platform also offers pre-programmed and ready-to-use MOVIKIT® software modules. These are used for performing automation and motion control tasks, from positioning to robotics. “The MOVIKIT software modules simply need to be configured using a graphical user interface,” says Sieberhagen. “So, there’s no requirement for programming by our customers. They achieve their goals much faster and save valuable time and money.”
Sieberhagen also points out that electric motors are one of the largest energy consumers globally. On the upside, this offers great potential for energy savings. He says that to maximise this potential, it is important to consider the overall efficiency of a power drive system (PDS), consisting of the motor and frequency inverter. IES2, which MOVIMOT advanced achieves, is the highest efficiency class for a PDS, with losses at least 20% below those of the reference PDS of system efficiency IES1.
Local assembly and support
Sieberhagen emphasises the need for high levels of local support for in-demand products. “MOVIMOT advanced will be fully assembled here in Australia in 2024. As well as transferring valuable skills to Australia, this approach has the advantage of shorter delivery times for our customers,” he says. “It will enhance the high level of support that already exists around the country.”
With plentiful spare parts and fully trained staff already on hand at SEW-EURODRIVE’s service centres across the nation, quick turnaround times are the norm. The support includes 24/7 emergency breakdown assistance via the telephone hotline and a network of offices and service centres in Melbourne, Sydney, Brisbane, Townsville, Mackay, Adelaide and Perth.
For Sieberhagen, the flexibility, scalability, and efficiency of MOVI-C decentralised and MOVIMOT advanced are key. “What strikes me is the ability of the product to be an all-rounder and to be equipped with necessary options and accessories to solve multiple customer applications,” he says.
For more information, click here.
Digital retrofits driving a new era of sustainable buildings
From ageing riverfront towers to high-performance telecom hubs, Siemens is helping Australian...
Blue Connections IT achieves carbon neutrality through sustainable technology
Schneider Electric is celebrating a significant milestone in its partnership with Blue...
STABILISOR tech revolutionises air compressor operation
ELGi's STABILISOR technogy sets new standards in compressed air reliability, energy costs and...