A concrete solution to reduce construction industry emissions
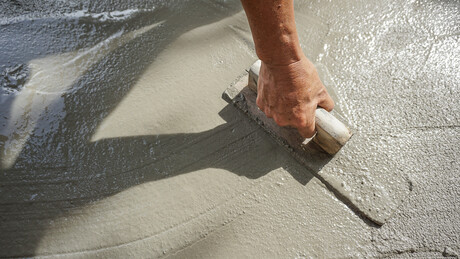
A recycled concrete solution developed by researchers at the University of Tokyo could reduce emissions from the construction industry. Calcium carbonate concrete is made from waste concrete and carbon dioxide from the air or industrial exhaust gases. It shows promise as a future construction material, especially in places where natural resources are limited.
It is estimated that around 7% of the world’s carbon dioxide emissions come from the manufacture and use of cement, the main component of concrete. And a large proportion of this 7% is due to the necessary use of calcium, which is usually obtained by burning limestone.
A new way to reduce emissions levels caused by concrete use has been proposed and proven to work by Professor Ippei Maruyama and C4S (Calcium Carbonate Circulation System for Construction) Project Manager Professor Takafumi Noguchi, both from the Department of Architecture at the University of Tokyo. They have found a way to take waste concrete and captured carbon dioxide, and combine them in a novel process into a usable form of concrete called calcium carbonate concrete.
Inspired by the way some aquatic organisms harden into fossils over time, Maruyama wondered if the same process that forms hard calcium carbonate deposits from dead organic matter could be applied to concrete. Calcium is essential for the reaction between cement and water to form concrete, and Maruyama saw this as an opportunity to investigate a less carbon-intensive way of performing the same function.
“Our concept is to acquire calcium from discarded concrete, which is otherwise going to waste,” Maruyama said. “We combine this with carbon dioxide from industrial exhaust or even from the air. And we do this at much lower temperatures than those used to extract calcium from limestone at present.”
Calcium carbonate is a stable material, so makes for a durable construction material. And the ability to recycle large quantities of material and waste is a great benefit. However, calcium carbonate concrete cannot replace typical concrete at present. It is not quite as strong as typical concrete, though for some construction projects, such as small houses, this would not be a problem. Also at present, only small blocks a few centimetres in length have been made.
“It is exciting to make progress in this area, but there are still many challenges to overcome,” Noguchi said. “As well as increasing the strength and size limits of calcium carbonate concrete, it would be even better if we could further reduce the energy use of the production process. However, we hope that in the coming decades, carbon-neutral calcium carbonate concrete will become the mainstream type of concrete and will be one of the solutions to climate change.”
The research paper has been published in the Journal of Advanced Concrete Technology.
igus E2.1 range with igumid CG LW
The igus E2.1 energy chain series is switching to the recycled material known as igumid CG LW,...
Vertiv CoolLoop Trim Cooler
The Vertiv CoolLoop Trim Cooler is designed to operate with fluctuating water temperatures...
Ecoforest heat pumps
Suitable for a wide range of building sizes and applications, Ecoforest heat pumps offer scalable...