Simple technology for solids removal from industrial and municipal wastewater
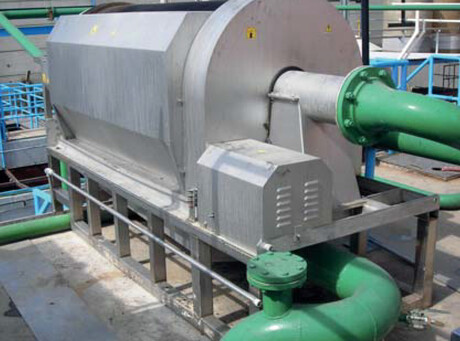
Simple, efficient, easily operated and maintained screening is the first and very critical stage in municipal and industrial wastewater treatment, as engineers and operators of food and beverage processing plants and abattoirs keenly appreciate.
Horizontal and Rotary Drum Screens are the ideal first line defence, because they capture suspended and floating solids that would otherwise flow through into the wastewater treatment plant. They reduce load and potentially recover valuable material and prevent downstream equipment damage and blockages.
Typical industrial applications using Rotary Wedgewire Drum Screens include general food processing (vegetables, fruit, coffee, starch processing), beverages (beer, wine, juice, soft drinks), slaughterhouses and abattoirs, tanneries, pulp and paper mills, textile plants, plastic manufacturers, or any industry where solids removal or recovery is needed.
In all these applications, there is a variety of materials that can clog downstream systems and wreak havoc — in some cases this material can be recovered as a valuable by-product as well as reducing load to the treatment process.
Rotary Drum Screens are the first line of defence to help prevent such clogging and associated issues. While it is true that most pumps and other systems are engineered to handle these, they still are the major cause of equipment and process failure, resulting in high wear, downtime, and cost.
Unless solids are efficiently separated out from wastewater at the start of the purification process, you are inviting trouble into the system. This can cost dearly in terms of downtime, environmental risk, clean-up costs and OH&S hazards for the operator teams involved.
This means ease of maintenance of headworks is a key consideration in preventing trouble, especially for municipalities and smaller industrial concerns operating on tight budgets. These entities also do not have the financial resources or large engineering teams to implement complex technologies for wastewater treatment.
Flexibility is also key to ongoing efficiency in handling diverse inputs and flows, regardless of the location and input. Headworks that are efficient over diverse conditions — that don’t fail when you need them most, such as under high load or flow — are vital to all the downstream purification and recycling process stages in a properly engineered wastewater treatment plant.
As a result of our experience over more than 30 years of wastewater installation and operational experience throughout the Asia-Pacific region, we have taken a different path to many in producing our different headworks designs for municipal and industrial applications to prepare for a future that is already arriving.
Horizontal In-Channel Drum Screen Advantages
Our engineering approach is not one-size-fits-all, because one size (or type) does not. Our horizontal in-channel rotary drum screening technology is primarily used on municipal applications and built to be both robust, reliable, and adaptable. They may not to be the cheapest up front, but do not end up transferring cost and problems down the line.
This whole-of-life cost, as distinct from a race to the bottom on sticker price, is the mature engineering approach to meet clients’ long-term objectives.
The screens are designed with all parts located above the wastewater flow, for simple operation and maintenance, with routine servicing possible without removing the drum.
Robust engineering, design, and stainless-steel construction all mean that these rotary drum screens have long service lives with low maintenance requirements. No mechanical components come into contact with screened solids, so there is no opportunity for premature wear from solids impacting internal workings of the screen.
Some non-technical people, who don’t have to live with the results of their decisions, might say “So what?”. We are not addressing them but the guys on the front line, the operators, and engineers, who will have a different view. That’s why we present our engineering and operational principles for a mature and timely discussion.
There are common features we embrace that are universally beneficial to WWTPs expected to perform and keep on performing.
Compared with typical traditional screening at wastewater treatment plants, for example, our in-channel technology has a low hydraulic profile and head loss at peak flows to increase solids removal efficiency.
When dealing with fine screening of larger flows, this technology has the advantage of mechanical simplicity, self-cleaning and high-efficiency screening. This results in reduced maintenance and cheaper whole-of-life costs compared with other types of screens, such as band and inclined drum screen designs.
Rotary Drum Screen advantages
CST’s above channel Rotary Drum Screens are traditionally used for the more heavily loaded industrial applications, although they are also used for municipal duty using 0.5–3 mm or finer screening.
Most industrial installations such as paper mills, food, beverage, and abattoirs, commonly use wedgewire apertures of 0.5–1 mm, whereas municipal would more commonly use 3 mm for primary treatment. They are also available with 2.0 mm holes on pre-MBR secondary fine screening for membrane protection.
Robust engineering, design, and stainless-steel construction all mean that these rotary drum screens have long service lives with low maintenance requirements. No mechanical components come into contact with screened solids, so there is no opportunity for premature wear from solids impacting internal workings of the screen.
Local manufacturing
One final way in which we have a different approach is our move to local manufacture closer to the place of use throughout the Asia-Pacific.
This move comes as intensifying supply chain issues interrupt, delay and lessen the supply of some of vital wastewater treatment technology, which is key to the sustainability and environmental performance of industrial and municipal wastewater treatment plants and key to their overall reliability in delivering services.
Not only does local manufacture deliver a more robust and low-maintenance product — and better whole-of-lifecycle value — but it places the customer next to the source of supply for spare parts, future extensions, and retrofits to boost performance long-term.
The switch to local production also enables us to offer full stainless-steel products with world-respected standards of Australasian metals engineering, replacing carbon steel components and further improving corrosion resistance in harsh local environments.
So if you are interested in the future, if our different engineering approach attracts you, we would value your observations and experience. Good engineering is an ongoing discussion, which we are keen to extend and develop in the light of real experience and vision.
No More Blockages for Western Sydney Meat Works after Gorman-Rupp Pump Upgrade
Hydro Innovations was engaged to provide a pump solution to replace an existing submersible pump...
Transforming Abattoir Wastewater Management with Smart Pump Solutions
For a seasoned operator in the abattoir industry, finding the perfect balance of safety,...
Wannon Water solves pump blockage issue
Wannon Water in Victoria sucessfully trialled Gorman-Rupp's solids handling technology to...