Sludge screens help Sydney Water produce biogas from sewage
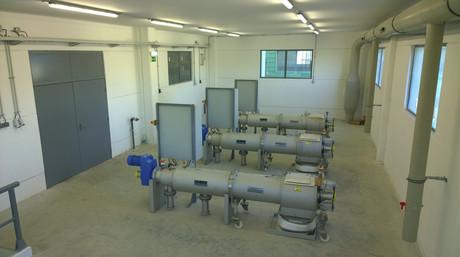
STRAINPRESS technology from Hydroflux HUBER is playing a small but vital part in helping Sydney Water achieve its goal of making a number of improvements at its Malabar sewage treatment plant. One of the major benefits will be an improvement in the quality of biosolids produced.
The Malabar STP, which processes nearly half of the city’s sewage through its primary treatment processes, produces about 33,000 tonnes a year of nutrient-rich biosolids — a soil conditioner/fertiliser which is used extensively to improve the fertility and structure of farming soils in NSW. These biosolids can produce green energy in the form of biogas.
“To increase the performance and efficiency of anaerobic digesters that process the biosolids, Hydroflux HUBER supplied the Malabar STP with three HUBER STRAINPRESS sludge screens,” said John Koumoukelis, a director of Hydroflux HUBER.
“These STRAINPRESS sludge screens have been operating for six months and are successfully removing unwanted screenings such as plastics, fine rags and cotton buds from biosolids before it is processed in the anaerobic digesters. These materials would also block mixers, heat exchangers and sludge pumps that are installed within the digesters.
“These unwanted materials would otherwise accumulate within the digester, leading to a reduction in performance, maintenance headaches and a reduction in the amount of gas produced.”
The STRAINPRESS sludge screen is a pressure-fed inline system for screening any type of sludge, including highly viscous and greasy waste. Said to increase the reliability of downstream sludge treatment systems and to reduce maintenance requirements, it consists of inlet and screening zone, a press zone and a discharge section.
A pump presses the liquid through the screening zone and delivers it to further process steps or utilisation. The liquid is under pressure. The coarse material, which is retained on the screen surface, is stripped off by a coaxial screw and pushed through the press zone, where the material is extensively dewatered and compacted. The compacted material is pressed through a gap around a hydraulically operated pressure cone, which closes part of the pipe end and builds up counter pressure.
The system does not need any wash water, as backwashing of the screen is unnecessary. The perforation and design of the discharge section are individually adjusted to suit specific requirements and it is easy to integrate the product into the existing pipeline and automatic system.
“One of the major benefits of STRAINPRESS is that it prolongs the need to put a digester offline for cleaning by many years — so the three sludge screens will make a major contribution to minimising the maintenance costs at the Malabar STP,” said Koumoukelis.
Phone: 02 9089 8833
Rosemount 490A optical dissolved oxygen sensor
The sensor is a digital Modbus-enabled measurement device designed to improve operational...
Kaeser GBS series rotary screw blowers
This range of blowers offers high efficiency and low maintenance and is suitable for applications...
Odosense Odour Emissions Tracking System
Odosense is an active odour analysis and public complaint validation system, which is suitable...