Turning bioplastic into valuable product
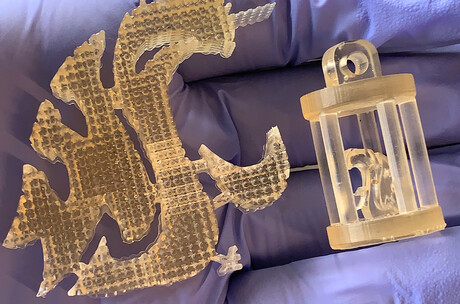
Washington State University scientists have developed a way of converting polylactic acid (PLA), a bio-based plastic that is used in filament, plastic cutlery and food packaging, into a printable resin by breaking it down into its constituent chemicals.
“We found a way to immediately turn this into something that’s stronger and better, and we hope that will provide people the incentive to upcycle this stuff instead of just toss it away,” said Yu-Chung Chang, a postdoctoral researcher in the WSU School of Mechanical and Materials Engineering and a co-corresponding author on the work. “We made stronger materials just straight out of trash. We believe this could be a great opportunity.”
Although it’s bio-based, PLA is categorised as a number seven plastic that doesn’t break down easily. It can float in fresh or salt water for a year without degrading. It is also rarely recycled because, like many plastics, when it’s melted down and re-formed it doesn’t perform as well as the original version and becomes less valuable.
“It’s biodegradable and compostable, but once you look into it, it turns out that it can take up to 100 years for it to decompose in a landfill,” Chang said. “In reality, it still creates a lot of pollution. We want to make sure that when we do start producing PLA on the million-tons scale, we will know how to deal with it.”
The researchers describe their method in the journal Green Chemistry. It involves breaking down the long-chain of molecules that makes up the PLA into the monomers which are used as basic building blocks of other plastics.
The method does not require high temperatures and takes about two days to complete. Additionally, aminoethanol, the chemical that is used to break down the PLA, is fairly inexpensive.
“If you want to rebuild a Lego castle into a car, you have to break it down brick by brick,” Chang said. “That’s what we did. The aminoethanol precision-cut the PLA back to a monomer, and once it’s back to a monomer, the sky’s the limit because you can re-polymerise it into something stronger.”
When the basic building blocks have been extracted from the PLA, they can be chemically reorganised into a liquid resin to be used as an ink for 3D printers. Testing revealed that the ink was as strong as those commercially available, meaning that these plastics could be recycled as a way of producing stronger material.
The researchers believe they will be able to apply their method to the recycling of polyethylene terephthalate (PET) plastic, as it is chemically similar to PLA, and hope to pursue this in the future.
REDWAVE TEX textile sorting solution
The REDWAVE TEX is a flexible sorting solution designed specifically for the textile industry.
PCO.Tech pco.pixelfly 1.3 SWIR camera
The pco.pixelfly 1.3 SWIR is a machine vision camera with an InGaAs image sensor that is...
Emi Controls V12so Odour Control Cannon
The V12so Odour Control Cannon combines four different functions in one machine — eliminate...