Beer waste gets a second life
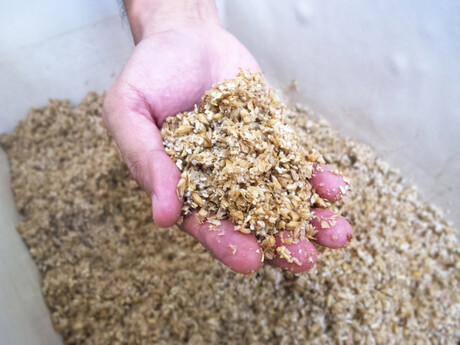
Beer making involves extracting flavour from barley and other grains, leaving behind a protein- and fibre-rich powder that is typically destined for cattle feed or landfill. But researchers from Virginia Polytechnic and State University have found a way to extract the protein and fibre from the spent grain and use it to create new types of protein sources and biofuels. The research will be presented at the spring meeting of the American Chemical Society (ACS), being held online from 5–30 April 2021.
“There is a critical need in the brewing industry to reduce waste,” principal investigator Haibo Huang said. His team partnered with local breweries to find a way to transform leftover grain into value-added products.
“Spent grain has a very high percentage of protein compared to other agricultural waste, so our goal was to find a novel way to extract and use it,” said graduate student Yanhong He.
Craft brewing has grown in popularity in the US, generating a major uptick in waste material from breweries, 85% of which is spent grain — comprising up to 30% protein and up to 70% fibre. Although cows and other animals may be able to digest spent grain, it is difficult for humans to digest it because of its high fibre content.
Huang and He developed a novel wet milling fractionation process to separate the protein from the fibre, an efficient process that does not require the grain to be dried first. The researchers tested three commercially available enzymes — alcalase, neutrase and pepsin — finding that alcalase provided the best separation without losing large amounts of either component. After a sieving step, the result was a protein concentrate and a fibre-rich product. Up to 83% of the protein in the spent grain was recaptured in the protein concentrate, which could be used as an ingredient in food products.
The extracted fibre was converted into fuel by pretreating the material with sulfuric acid and breaking it down into sugars from cellulose and hemicellulose. Feeding the sugars to a species of Bacillus lichenformis, a microbe discovered by postdoctoral researcher Joshua O’Hair, produced 2,3-Butanediol, a compound used to make products including synthetic rubber, plasticisers and 2-Butanol.
The team hopes to find suitable enzymes and green chemicals to make this process even more sustainable, scalable and affordable.
REDWAVE TEX textile sorting solution
The REDWAVE TEX is a flexible sorting solution designed specifically for the textile industry.
PCO.Tech pco.pixelfly 1.3 SWIR camera
The pco.pixelfly 1.3 SWIR is a machine vision camera with an InGaAs image sensor that is...
Emi Controls V12so Odour Control Cannon
The V12so Odour Control Cannon combines four different functions in one machine — eliminate...