Hume opens door to energy efficiency
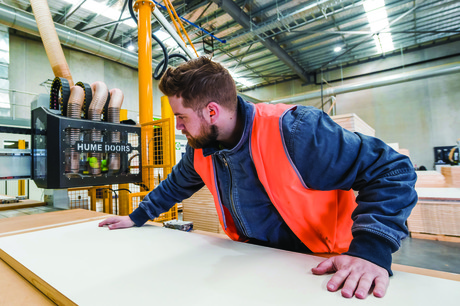
Door manufacturer Hume Doors & Timber provides innovative doorway technology for the building industry. With an extensive range of products and operations in every capital city in Australia and New Zealand, as well as strategically placed regional branches, Hume delivers specialist low-volume to mass high-volume production.
Committed to operating its entire business in an environmentally sustainable manner, Hume’s manufacturing and distribution processes have been designed to minimise the company’s environmental footprint. Innovation, sustainability, energy efficiency and recycling all play a key role in the manufacturing facilities. With compressed air systems found across Hume’s manufacturing process — responsible for powering the woodworking machinery such as the sanders and staple gun — the company has opted for compressed air equipment that is reliable and energy efficient.
An increased demand for compressed air came when Hume expanded its manufacturing operation in Sydney. With the existing system unable to meet demand, Hume General Manager Eddie Luke contacted longstanding compressed air supplier Kaeser Compressors for a solution. Kaeser recommended and installed a CSD 125 rotary screw compressor. The CSD series of rotary screw compressors provide significant energy savings in four key ways:
- Each CSD system features a rotary screw compressor block featuring Kaeser’s energy-saving Sigma Profile rotors. Operating at low speed, the compressor blocks are equipped with flow-optimised rotors for high efficiency. The newly refined rotors found in the latest-generation models, together with additional optimisation measures such as reduced pressure losses, deliver between 3 and 6% improved power performance compared with previous models.
- Kaeser’s 1:1 drive design eliminates transmission losses associated with gear or V-belt driven systems.
- An IE4 efficiency drive motor further maximises energy efficiency. IE4 motors comply with and exceed prevailing Australian GEMS regulations for three-phase electric motors.
- The Sigma Control 2 industrial PC-based internal controller ensures efficient control and system monitoring, adjusting flow rate to match actual compressed air demand and thereby providing further energy savings.
“We have opted for Kaeser compressors for many years in our manufacturing facilities,” Luke said. “In fact, we have one Kaeser that has been reliably in operation now for over 15 years! We have also realised energy savings over the years by opting for Kaeser compressors.”
Phone: 1800 640 611
ABB Battery Energy Storage Systems-as-a-Service
ABB has launched its new BESS-as-a-Service — a flexible, zero-CapEx solution...
Mitsubishi Electric FR-D800 series inverters
The FR-D800 series inverters are designed for a range of industrial applications.
Trina Solar Elementa 2 Pro 5MWh battery storage solution
Trina Solar has launched the Elementa 2 Pro 5MWh battery energy storage solution, building...